环氧树脂网(www.epoxy8.com)最新报道[此消息来源于网络]。
杜建伟1,范云鹏2
(1.天津中油渤星工程科技有限公司,天津300451;2.中国石油集团工程技术研究院,天津300451)
摘要:介绍了高固含环氧防腐蚀涂料、无溶剂环氧防腐蚀涂料和水性环氧防腐蚀涂料的国内外研究情况、目前存在的问题和发展方向,提出了3类环保型环氧防腐蚀涂料的发展趋势。
关键词:防腐蚀;环氧;环保
中图分类号:TQ637 文献标识码:A 文章编号:1007-9548(2011)09-0011-05
0引言
环氧树脂是含有环氧基团的高分子物质,主要是由环氧氯丙烷和双酚A合成的,是线性分子结构,依靠结构中的羟基和环氧基与诸如酚醛树脂、聚酰胺树脂、多异氰酸酯、酸酐等发生反应而形成不同性能的环氧树脂涂料涂层,环氧树脂的分子结构决定了环氧系涂料具有优异的耐化学性、很强的黏结力。在防腐蚀涂料中占有重要的地位。但目前市场上采用的环氧防腐蚀涂料仍以传统溶剂型防腐蚀涂料为主。
近年来,世界各国相继提出了有关环境污染限制的法律与法规,其中涉及涂料行业的就有涂料中有机挥发物的含量和有害空气中的污染物两大问题,这样将使占整个世界涂料行业中53%的溶剂型涂料的生产受到限制。
欧共体1993年颁布了《生态管理和审核法规》(EMAS),并于1994年4月生效。特别是美国,在1992年就发布有关法令,制定环境管理的国家标准,并于1994年进行修订。AIM条例的核心就是限制VOC,逐步走向零VOC。据有关资料表明,日本也开始将21世纪的工作重点放在发展环境友好的涂料中。因此,保护环境将成为世界性的话题[1]。
安全问题对国家、行业、部门来说同样是很重要的,涂料的挥发性有机物大都易燃易爆,因此其在生产、施工、运输和存放过程中都潜存着安全隐患。因此,开展低VOC防腐蚀涂料的研究很有必要。实现低VOC的途径主要为大力发展高固体分涂料、水性涂料、粉末涂料和辐射固化涂料等新型涂料[2]。本文主要介绍呈液体状态的高固体分环氧防腐蚀涂料、无溶剂环氧防腐蚀涂料和水性环氧防腐蚀涂料目前需要解决的问题以及发展方向。
1高固体分环氧防腐蚀涂料
对于高固体分的定义,至今还没有统一的标准,我国多采用质量分数作为衡量标准,而国外多采用体积分数作为标准。一般认为固体含量在70%以上的涂料是高固体分涂料[3]。该类涂料虽然降低了挥发性有机物的排放,但仍然存在一些溶剂,严格意义上说高固体分涂料仍对环境有一定的危害。但由于其施工方便,物化性能优异,目前仍是环氧防腐蚀涂料的主打产品。
1.1高固体分环氧防腐蚀涂料的国内外研究现状
早期采用的环氧树脂防腐蚀涂料主要是以E-12环氧树脂为主要成膜物,受施工工艺限制,涂料达到适于施工的黏度后,固体含量一般低于70%。20世纪80年代许多涂料研究者采用E-44和E-42代替E-12环氧树脂,使环氧涂料的固体含量达80%以上。如海军后勤学院的H87环氧树脂涂料和石油工程技术研究所的8701环氧树脂涂料,不仅涂料固体含量超过80%,而且涂层具有优异的物化性能,尤其是对油田污水具有长效的耐腐蚀性,是20世纪80年代较为优异的高固体分环氧防腐蚀涂料。
自高固体环氧防腐蚀涂料研制成功以来,该类材料在国内外得到空前的发展,研究工作也在不断开展。如郑耀臣以原料配比、催化剂用量等因素对配方性能的影响为基础制备了环氧厚浆涂料[4]。李翠英等通过涂料各组分、涂膜厚度等对涂膜性能的影响制备出低温固化、高固体分环氧饮水设备用防腐涂料[5]。彭志强设计了具有超低VOC的新型高固体分环氧煤焦沥青砂浆涂料[6]。刘俊峰采用改性环氧和聚氨酯预聚物制备的高性能高固体分涂料一次涂覆厚度在150μm以上,同等条件下涂层中针孔数量比普通防腐蚀涂料少2/3以上[7]。谢国先等利用反射红外(RAIR)对氨基硅烷偶联剂的作用机理分析研究了硅烷偶联剂对高固体分环氧涂层附着力的影响[8]。正是由于这些源源不断的研究工作,使得该材料在防腐蚀领域得到空前的发展。
1.2高固体分环氧防腐蚀涂料存在的问题
高固体分环氧防腐蚀涂料以其优异的物理机械性能和抗化学介质侵蚀性能以及方便的施工性能,虽然已在防腐蚀领域占着重要的地位,但是仍存在一些问题。主要如下:
⑴高固体分涂料中仍含有一定量的挥发性有机溶剂,对环境和人体有一定的危害性,不符合环保要求。
⑵高固体分涂料中溶剂含量虽较低,但不能排除其易燃易爆性,生产、施工、运输以及存放仍然存在安全隐患。
⑶高固体分涂料一次成膜厚时,由于溶剂的存在容易出现针孔、流平差、表干里不干等涂层弊端。
1.3高固体分环氧防腐蚀涂料的发展方向
从高固体分环氧涂料存在的问题可以看出,这些问题的存在都是因为涂料中存在溶剂所致。因此高固体分环氧涂料的发展方向是开发不含挥发性溶剂的无溶剂液态环氧防腐蚀涂料。
2无溶剂环氧防腐蚀涂料
无溶剂环氧防腐蚀涂料目前国内外主要分为2类,一类是以采用中高相对分子质量的固体环氧树脂制成的固态粉末状的粉末涂料;另一类即是用反应性活性稀释剂替代溶剂的液态无溶剂环氧涂料。前者的生产、施工和固化与常规溶剂型涂料不同,这里不再叙述。本文提到的无溶剂环氧防腐蚀涂料主要是指后者,其理论固体含量达100%,常温固化检测值接近100%,采用GB/T1725测得固体含量也在95%以上。
无溶剂液态环氧树脂涂料是一种不含挥发性有机溶剂的环保型涂料。施工时可采用喷涂、刷涂或辊涂。由于不含溶剂避免了溶剂挥发而造成的火灾危险、溶剂中毒以及污染环境大气的危害,同时也避免了因溶剂挥发而造成的漆膜弊端。
2.1无溶剂环氧防腐蚀涂料国内外研究现状 实现液态无溶剂环氧防腐蚀的途径是采用反应性活性稀释剂代替挥发性有机溶剂。活性稀释剂具有环氧基,能参与环氧树脂的固化反应,同时还起着降低涂料黏度的作用。由于活性稀释剂参与反应而避免了溶剂的挥发实现涂料的无溶剂化。用于环氧树脂涂料的活性稀释剂主要有单缩水、双缩水和三缩水几类。目前国内外常用的活性稀释剂见表1。
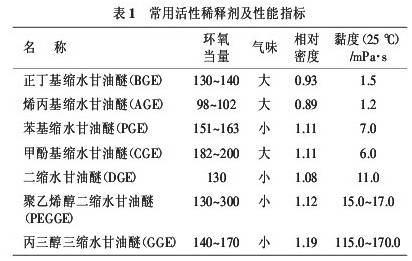
表1 常用的活性稀释剂及性能指标
随着活性稀释剂品种的增多,液态无溶剂环氧防腐蚀涂料性能越来越完善,相应地关于这方面的研制工作也越来越多。王D等通过高、低相对分子质量环氧树脂的搭配添加适量的硅基聚合剂制得了无溶剂超厚膜型环氧重防腐涂料,其一次喷涂厚度可达1200μm[9];杜建伟等以合成的活性稀释剂与相对分子质量小的环氧树脂协同特定固化剂反应而得超厚膜无溶剂环氧涂料,在工程上得到良好应用[10];常玉等根据不同用途采用氢化双酚A型环氧树脂或脂肪族环氧树脂作基料,控制活性稀释剂用量在20%而制成无溶剂环氧自流平地坪涂料,并获得了良好的应用[11];欧国勇等采用丁基缩水甘油醚作活性稀释剂制成无溶剂防静电自流平地坪涂料并获得良好应用[12];朱怀刚等采用双酚A型的相对分子质量低的液体环氧树脂和四针状氧化锌晶须制成抗静电效果持久的耐磨、耐压、耐化学腐蚀的无溶剂防静电自流平地坪涂料[13];李杰等以环氧树脂作为主要成膜物质,加入石油沥青以解决与旧涂层搭接的问题研制了一种无溶剂环氧石油沥青重防腐蚀涂料[14];黄丽等选用低黏度环氧树脂制备无溶剂防腐涂料,通过正交试验取得了耐酸性较好的优化配比,结果表明固化剂是影响涂料耐酸性的主要因素,应用正交试验方法缩短了试验时间[15]。
2.2无溶剂环氧防腐蚀涂料存在的问题
无溶剂液态环氧防腐蚀涂料随着活性稀释剂品种的日益增多和环氧以及固化剂黏度的进一步降低,目前该类涂料在防腐蚀领域已占据一定的份额。并具有逐步取代厚浆型溶剂型环氧涂料的趋势。但目前仍然存在一些难以解决的问题,具体如下:
1)无溶剂液态环氧防腐蚀涂料由于没有溶剂挥发,施工时A、B两组分混合均匀后,反应即开始发生。随着反应发生,涂料的黏度急剧上升,在短时间内即无法施工,也就是说涂料的施工使用期较短。研究人员,为了解决这一问题采用延缓反应速度的方法,但这一方法又使得涂料的表面干燥时间较长给施工带来麻烦。也就是说施工使用期和表干时间之间的矛盾一直无法很好地解决。
2)为解决上面问题采用专用设备即双组分喷涂设备带来了设备投资大的问题,同时这种专用设备需要在固定场所安装施工。对于防腐施工而言有许多是在现场进行。因此,仍然没有完全解决涂料因使用期短而带来的施工问题。
3)无溶剂液态环氧防腐蚀涂料由于活性稀释剂和环氧树脂协同与固化剂反应最后形成的成膜物,同相对分子质量较高的溶剂型环氧涂料对比,涂层的物理机械性能稍差。另外无溶剂环氧涂料固化反应程度不宜得到大幅度的提高,极难达到90%以上,因此,其抗阴极剥离性能稍差一些。
2.3无溶剂环氧防腐蚀涂料的发展方向
从目前无溶剂液态环氧防腐蚀涂料存在的问题可以看出,无溶剂环氧防腐蚀涂料今后研究的重点应是解决表干时间和涂料施工使用期的矛盾,即开发紫外光加速固化反应类无溶剂液态环氧防腐蚀涂料和移动式双组分喷涂设备等方面的研究。同时也可在扩大无溶剂环氧涂料的应用领域方面开发研究,如耐候性、抗阴极剥离性等。
3水性环氧防腐蚀涂料
随着人们对环境保护的关注,环氧涂料除了以粉末及无溶剂形态出现外也开发了水性涂料。实用的有烘干型的阴极电沉积漆CED、阳极电沉积漆AED,均以环氧树脂为主要基料,此外以Glidden公司开发的水性丙烯酸接枝的环氧涂料最为成功,现已广泛应用。实用中常温固化型大多是双组分水乳化涂料[16]。目前,市场上广泛使用的水性环氧涂料主要由两组分组成,疏水性的环氧树脂和亲水性的胺类固化剂。
3.1水性环氧涂料的国内外研究现状
水性涂料最早在建筑领域得到了广泛应用,随后才推广应用于钢结构防腐涂料。水性环氧涂料是目前用于工业重防腐领域最为成功的涂料品种之一。国外从20世纪70年代已开始着手对环氧树脂进行水性化的研究,水性环氧从早期的外加乳化剂到现在的环氧自乳化或水可分散体系的开发,克服了外加乳化剂水性环氧的缺点,延长了水性环氧体系的适用期,改善了体系的耐水性等,使性能更接近于溶剂型环氧。目前已开发了许多品种,大量用于水泥制品修补剂、防水涂层、汽车维修底漆、钢结构的防腐蚀等,特别在密闭船舱施工方面具有环保和无毒安全的优势[17]。
韩峰等利用化学接枝法将环氧树脂接枝于丙烯酸及其酯的共聚物上,形成具有一定交联度、能分散于水中的自乳化树脂,其涂膜具有优良的耐碱性与耐盐雾性[18]。杨瑞影等采用对氨基苯甲酸对环氧树脂部分环氧键进行开环引羧,再加安全型皂化剂和活性分散剂皂化分散处理制备水性环氧树脂乳液,研制出双组分、室温固化、环保和防腐性能优异的牺牲型水性环氧防腐涂料[19]。ElmoreJimD等开发的双组分水性涂料技术将可室温固化的胺固化剂用于金属防护涂料,以非离子分散涂料代替了离子分散涂料,环氧/胺树脂能快速聚结、相互溶解,使用稳定的、与水相容的添加剂和过滤料使非离子环氧/胺树脂加以完善[20]。Walker等研制了一种多层包装材料,它主要由透气材料层和至少一层阻气涂料构成,该涂料是通过多官能度的环氧化合物和水在酸存在下共聚而得的聚合物多元醇。该涂料可克服塑料包装材料阻气性较差的不足[21]。此外,由于水性环氧树脂涂料具有优良的力学性能和与水泥良好的配伍性,因此可以制备高强混凝土,其中水性环氧树脂作为辅助成分加到混凝土或水泥砂浆中,可提高混凝土的抗渗性。水性环氧树脂涂料可与其他通用乳液(如聚丙烯酸乳液、水性聚氨酯)配合使用,协同效应较好,可以得到具有不同性能的涂层[22]。
3.2水性环氧涂料存在的问题
水性环氧涂料的优点是显而易见的,但常温固化施工型水性环氧涂料在防腐蚀领域的应用一直未得到广泛推广,主要原因是存在如下问题:
1)水性环氧树脂固化不充分影响其防腐蚀性能。水性环氧分散相粒子尺寸较大时,粒子表面的固化剂浓度相对较高,导致表面快速固化,随着固化反应的进行,环氧树脂分散相的表观黏度不断增大,Tg也会逐渐提高,固化剂分子向环氧树脂粒子内部扩散速度逐渐变慢,环氧树脂粒子内部来不及固化而致使涂膜固化不完全。固化剂与环氧树脂的相容性不稳定,原因是固化剂水溶体系和环氧涂料水溶体系不完全一致,尤其是当一个组分为水溶另一组分为树脂体系时更易发生。
2)水性涂料在低温高湿等环境下干燥固化速度非常慢。原因是水的蒸发热高,在低温和高湿情况下,水蒸发慢,延长干燥时间。尤其是在0℃以下涂料施工后尚未成膜就上冻成冰,无法进行施工。
3)防腐施工现场条件复杂,有时很难避免存放涂料温度低于0℃的情况,在低于0℃的情况下可能会造成涂料的变质。
4)价格问题,由于水性环氧涂料需要经过一定的方法处理使本不水溶的树脂体系变成水溶的以利于施工,当涂料涂刷后随着水分的挥发逐渐固化成膜。因此,相比较而言达到同等厚度的涂层水性环氧涂料的价格要比溶剂型和无溶剂型环氧涂料要高一些。
5)闪蚀和润湿较差问题。在钢铁表面施工时,由于水的电导率高,易使钢铁发生腐蚀,即涂膜干燥过程中的闪蚀问题。水的表面张力较高,这对基材和颜填料的润湿造成困难,尤其除油不干净的底材更难润湿。
6)颜填料在水性环氧涂料中的分散稳定性较溶剂型涂料差,易于聚集沉淀。而防锈颜料常常是靠微弱的水溶作用来发挥其功能的,因此,水性环氧涂料可用的防锈颜料受到一定的限制。
3.3水性环氧涂料的发展方向
针对以上水性环氧涂料存在的问题,今后应把如何解决这些问题作为该类涂料的发展方向。
4结语
无论从环保还是从安全考虑,发展环保型环氧防腐蚀涂料应是时代发展的要求。高固体分环氧防腐蚀涂料只是一种过渡环保产品。随着无溶剂环氧防腐蚀涂料技术的日益完善必将逐步取代高固体分环氧防腐蚀涂料。因此,无溶剂型环氧防腐蚀涂料和水性环氧防腐蚀涂料应是具有实际意义的环保安全型产品。从目前这两大类涂料存在的问题看,无溶剂型环氧涂料除施工不方便外,其他性能均比水性环氧涂料要好一些。因此,应大力发展液态无溶剂环氧防腐蚀涂料,该类涂料重点解决涂料使用期短和表干时间过长的矛盾问题。水性涂料虽然尚存在一些问题,但因其施工方便仍具有一定的市场。
参考文献:
[1]孙凌.水性环氧涂料在防腐蚀领域中的应用探索[J].上海涂料,2000(4):46-48.
[2]赵志超,袁采登,徐涛,等.环保型环氧树脂涂料[J].热固性树脂,2005,20(6):32-35.
[3]向斌,杨永峰,韦奉.高固体分涂料的应用及发展趋势[J].现代涂料与涂装,2007,10(10):40-42.
[4]郑耀臣.环氧厚浆涂料的制备[J].涂料工业,2004,(34)11:26-28.
[5]李翠英,马兴,何桂兰,等.高固体分环氧饮水设备防腐涂料[J].现代涂料与涂装,2007,10(2):11-13.
[6]彭志强,高固体分环氧煤沥青砂浆涂料的研究及应用[J].上海涂料,2004(1):5-7.
[7]刘俊峰.高性能高固体分涂料的开发及应用[J].化工新型材料,1998(1):22-23.
[8]谢国先,邱大健,李朝阳,等.氨基硅烷偶联剂对环氧涂层附着力的影响[J].材料保护,2008,41(3):22-24.
[9]王D,李震,刘志,等.无溶剂超厚膜型环氧重防腐涂料的研制[J].中国涂料,2009(3):38-40.
[10]杜建伟,张静,梁镐,等.超厚膜无溶剂环氧涂料的研制[J].涂料工业,2007,37(2):8-9.
[11]常玉,梁剑锋,刘戎志.无溶剂环氧自流平地坪涂料技术探讨[J].涂料工业,2000,30(12):50-53.
[12]欧国勇,程启朝,朱庆坚.无溶剂防静电环氧自流平地坪涂料及涂装[J].现代涂料与涂装,2005,8(1):16-19.
[13]朱怀刚,刘戎治.新型无溶剂防静电环氧自流平地坪涂料[J].中国涂料,2004(4):22-24.
[14]李杰,陈群尧,李红旗,等.无溶剂环氧石油沥青重防蚀涂料研究[J].腐蚀与防护,1999,20(2):80-99.
[15]黄丽,郑华荣.环氧无溶剂防腐涂料耐酸性的研究[J].材料工程,2009(S2):161-163.
[16]虞兆年.涂料工艺[M].北京:化学工业出版社,1996.
[17]赵志超,袁才登,徐涛,等.环保型环氧树脂涂料[J].热固性树脂,2005,20(6):32-35.
[18]韩峰,陈志明,何青峰,等.水性环氧-丙烯酸树脂制备及其涂膜性能[J].涂料工业,2003,33(3):1-3.
[19]杨瑞影,万平玉,刘小光,等.牺牲型水性环氧防腐涂料的研究[J].涂料工业,2002,32(11):9-11.
[20] Elmore J D, Kincaid, Komarc P C, et al. Waterborne epoxyprotective coatings for metal [J]. J. Coat. Tech., 2002,74(931):63-72. [21] Walker F H, Pepe F R, Dickenson J B. Packaging materialshaving barrier coatings based on water -epoxy resin copoly-mers[P].US6777088,2004-08-17. [22] 陈铤,施雪珍,顾国芳.双组分水性环氧树脂涂料[J].高分子通报,2002(6):63-70. |
以上就是《浅谈液态环保型环氧防腐蚀涂料发展现状》的全部内容。 环氧树脂 - www.epoxy8.com -(责任编辑:admin) |